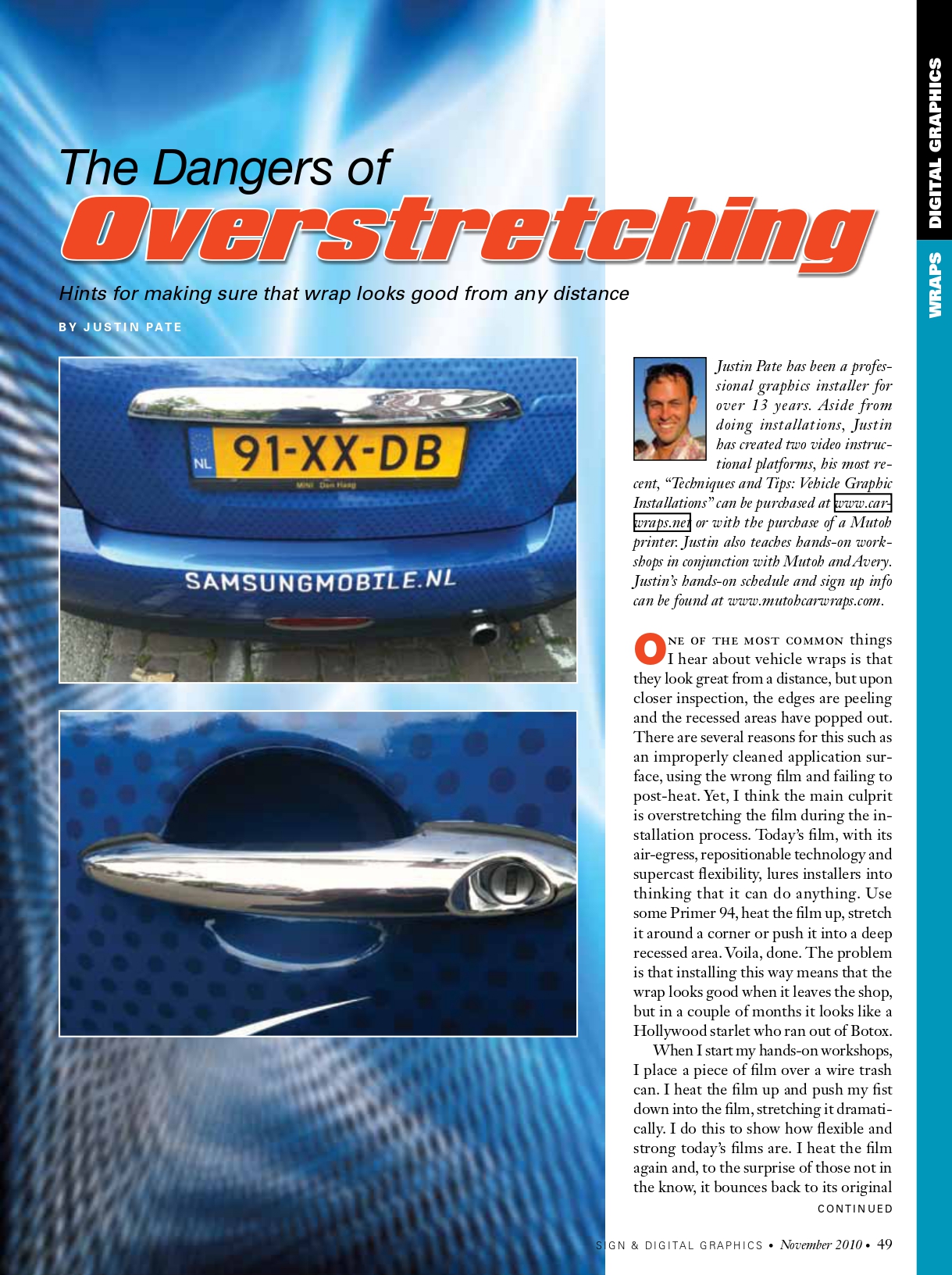
Overstreching
The Dangers of Overstreching
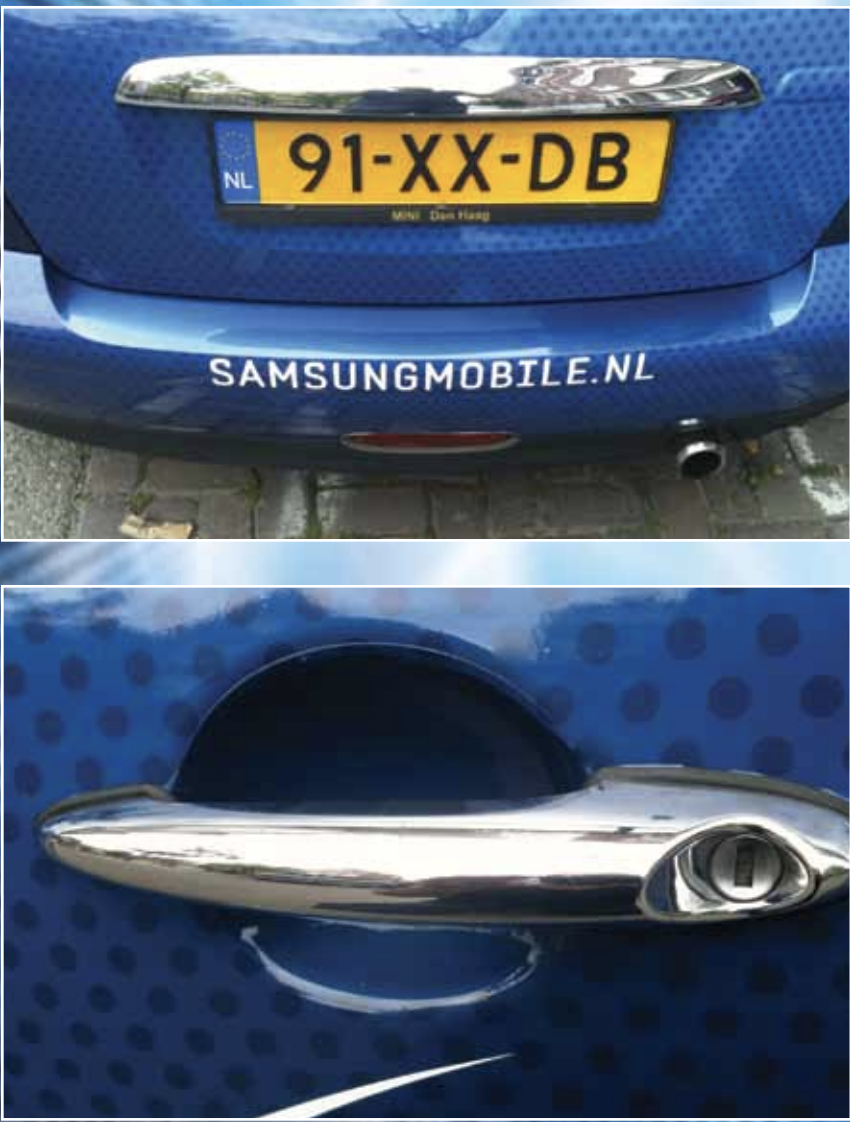
Justin Pate has been a professional graphics installer for over 13 years. Aside from doing installations, Justin has created two video instructional platforms, his most recent, "Techniques and Tips: Vehicle Graphic Installations" can be purchased at www.carwraps.net or with the purchase of a Mutoh printer. Justin also teaches hands-on workshops in conjunction with Mutoh and Avery. Justin's hands-on schedule and sign up info can be found at www.mutohcarwraps.com.
One of the most common things I hear about vehicle wraps is that they look great from a distance, but upon closer inspection, the edges are peeling and the recessed areas have popped out. There are several reasons for this such as an improperly cleaned application surface, using the wrongFilm and failing to post-heat. Yet, I think the main culprit is overstretching the Film during the installation process. Today's Film, with its air-egress, repositionable technology and supercast +exibility, lures installers into thinking that it can do anything. Use some Primer 94, heat the Film up, stretch it around a corner or push it into a deep recessed area. Voila, done. The problem is that installing this way means that the wrap looks good when it leaves the shop, but in a couple of months it looks like a Hollywood starlet who ran out of Botox.
When I start my hands-on workshops, I place a piece of Film over a wire trash can. I heat the Film up and push my Fist down into the Film, stretching it dramatically. I do this to show how +exible and strong today's Film are. I heat the Film again and, to the surprise of those not in the know, it bounces back to its original


shape and tension. The reason the Film does this is because it contains PVC. The chemical and physical properties of PVC give the Film memory. I tell the people in my workshops that this memory is both your friend and enemy. Overstretch the Film and it puts too much pressure on the adhesive to hold the position. Knowing how to walk the line between stretching and overstretching the film is key to durability, efficiency and profits.
I think the best example of how this relates to vehicles can be seen in a demonstration I came up with recently. One area on vehicles that tends to have the most peeling is on the corners. The reason for this is that the Film is pulled in many directions and the angles are generally extreme. When a lot of installers get to the corners, they are taught to heat
When installers say, "I tell my clients to stand 10 feet back" or "Imagine it moving at 40 mph." I understand this but I think it's a complacency that hurts the industry.
up the Film and then pull it with force onto the corner. Once the Film is on with this approach, I draw a line on the edge where the excess Filmwould get cut off. I then pull the Film back up and heat it again to trigger the memory, which brings it back to its original shape and tension. I then re-install the piece using sound squeegee techniques, well-placed relief cuts and directing the tension on the Film with wide Fingers and micro-adjustments. Once I apply the Film, I mark the edge again, which is always dramatically farther away from the overstretched line (between ½ - 1 inch). This discrepancy shows the difference between overstretching and applying the right way. In essence, it's the difference between the wrap looking good for only one month and being perfect for three years.
For me, my rule of thumb is to heat only when I absolutely have to. I minimize the need to heat and overstretch by using inlays, technique and having a buffer on my squeegee that is thin. Some examples are in the accompanying photos:
The front bumper of the red car is a difficult one. The reason for this is that it has deep recessed areas that have steep angles. Ideally, I would love to heat this area in with one piece so that it looks like paint. However, there are only one or two Films on the market that I would feel comfortable applying in one piece for a client. To avoid failures and peeling I opt to go the safe route and install well placed inlays.
First, I apply Film to the vertical columns and cut off the excess along the contour of the bottom section. I then apply Film to the +at areas on the bottom and sides. Again, I cut off the excess along the contours of the vehicle and overlap film on the column. I then apply the main area on the bumper, overlapping the insideFilm by about ¼ inch. The inlay approach means that I have overlaps but since I applied them from the inside out and followed the contours of the vehicle, the overlaps blend into the car and are hardly noticeable. This approach means that I don't overstretch the Film and I create durability while maintaining quality.
An example of how to avoid overstretching and create a project comes on a multi-vehicle job I recently did for Samsung. The campaign was for only three months so the printer used calendar Film, which is significantly cheaper than cast. He felt comfortable doing this because he made the design match with the colors of the vehicles and that I knew how to apply the Film without overstretching. How I avoided overstretching can be seen on the door handles and back bumper.
For the door handles, instead of trying to be a super installer, I didn't install the Film inside the door handle. This area is a deep recessed area that calendar Film cannot hold. To avoid failure, I cut off the Film along the contour of the inside area. By cutting with a perfect line, the paint of the vehicle blends into the print. I did the same thing for the back bumper. Can I wrap a bumper in one piece? Sure. Can I do it with calendar film? Sure, but it won't look good in a week. So, I cut off the top section along the contour of the bumper. This keeps me from overstretching the Film, I maintain quality and my client makes a project because he could use a Film that costs less.
For all of these examples and for all of my installs I now use a specific combination of buffers on my squeegees. For the +at areas I use a felt buffer called the Flexifelt. When I get to curves and challenging areas I use a Squeezy Sleeve. The reason I use these is that the Flexifelt glides along the Film easily and without scratching. However, the Flexifelt is wide due to the fact that it has an adhesive layer. This is why I then switch to the Squeezy Sleeve. It has a thin, hard edge that allows me to apply the Film farther than I could with a wider buffer and, most importantly, I use less heat, which keeps me from overstretching.
When installers say, "I tell my clients to stand 10 feet back" or "Imagine it moving at 40 mph." I understand this but I think it's a complacency that hurts the industry. It is an acceptance of a low standard of quality that can easily be raised if overstretching is elimniated. The keys are to really understand the potential and limits of all kinds of Films. Also, instead of relying on Primer 94 and install everything in one piece, use clean inlays to eliminate overstretching. Wrapping a bumper in one piece may seem like a "perfect install," but if it starts to peel and lift in a month then it's not perfect. It's no different than the Botox quick Fix. Perfection is a result of working smarter and more organically. Are you going for trashy Heidi Montag or French goddess "au natural" Brigitte Bardot?